Lithium battery production: the Flash Battery customisation process
11 August 2019
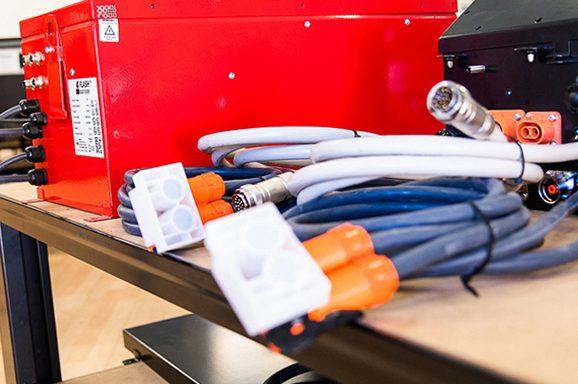
Customised lithium battery
8 customisation steps for your customised lithium battery
How do you customise production of a lithium battery pack?
Customising a lithium battery means understanding the customer’s requirements and designing ad hoc solutions for the type of use required.
We have produced over 500 different models of lithium battery, and each has followed the Flash Battery customisation protocol.
Flash Battery customers tend to be companies manufacturing industrial vehicles and/or machines who would like to switch from lead to lithium or from an internal combustion engine to an electric/hybrid engine and who need guidance through this technological change.
Lithium battery production
Lithium battery production: 15 weeks and 8 customisation steps
The first step for the production of a customised lithium battery pack is a free consultation with our marketing team who analyses the customer’s requirements and carries out an initial project feasibility analysis.
- Project feasibility analysis
- Collection of information/completing the order form : 1 WEEK
- Provisional order confirmation : 1 WEEK
- Drawing up and sending the supply specification : 3 WEEKS
- Supply specification approval / modifications update : 1 WEEK
- Completion of the Project Technical Folder : 2 WEEKS
- Sending of the order confirmation with the final delivery date : 5 WEEKS
- Battery pack production and testing : 2 WEEKS
1. Project feasibility analysis
The feasibility analysis is a free ad hoc consultation carried out according to the customer’s requirements and project.
During this initial phase, the sales team analyses the customer’s requirements (work cycles, application sector, voltage and capacity to mention just a few) and an initial solution for the customer’s problem is formulated.
Every detail which will be used to produce the Flash Battery customised lithium battery pack is contextualised so the economic context can also be quantified.
2. Collection of information / completing the order form
The strategic consultation phase deals with customer requirements and defines the technical data.
The marketing team collects all the detailed information necessary for the next steps in the supply.
The information collection form is completed, which contains the working specifications of the customised battery, the mechanical size, the most suitable connectors for the specific project and lastly how the various devices inside the machine/vehicle will communicate is defined.
3. Provisional order confirmation
The Flash Battery customer care office takes on the order and sends the customer a provisional order confirmation which indicates the general lead times.
The provisional order confirmation defines the various production steps and indicates the week when the lithium battery is estimated to be delivered, the week when the customer will receive the supply specifications and the week when the specifications must be approved.
Therefore, the production steps and timing needed to produce the customised battery pack are immediately clear to the customer.
4. Deawing up and sending the supply specification
To create a complete SDF, the marketing and customisation teams hold a kick off meeting to plan priorities and activities. The customisation team creates a project technical folder where the electrical and mechanical specifications of the battery pack are defined.
This documentation defines all the supply specifications: the nominal electrical and mechanical specifications of the lithium battery as well as functions, a 3D mechanical proof and wiring diagram.
5. Supply specification approval / modifications update
During this step, the customer confirms or asks for the supply specifications received from the Flash Battery customisation office to be updated or changed. At this point, the project is approved by both parties and can move on to the next step: completion of the Project Folder.
6. Completion of the project technical folder
Once the technical specifications have been approved by the customer, the customisation team completes the project technical folder which includes the electrical and mechanical production specifications and all the manuals necessary for the sale of the lithium battery pack (production specifications, documents for specific certifications and user manuals).
7. Sending of the order confirmation with the final delivery date
During this step, the Customisation team sends the order confirmation with the final delivery date and it makes sure that the material needed to produce the battery pack is supplied.
8. Battery pack production and testing
At this point, battery pack production starts according to the specifications. At the end of production, the battery pack is tested.
The test follows a specific check list for the lithium battery which includes charging and discharging cycles as well as the general functions of the battery pack
Once the test has been completed successfully, the battery pack is dispatched.
At the end of production, the Flash Battery battery pack is ready for shipping in compliance with the conditions established with the customer.
Our work does not end when the battery pack is shipped. After shipping, we carry out two important activities: Remote control and the Service Centre.
The battery pack is controlled remotely every day and the data from every charge and discharge cycle is sent to the Flash Data Centre where it is analysed automatically guaranteeing efficiency throughout the battery pack’s life.
If the battery pack does not include remote control, the Flash Battery Service Team is at the customer’s complete disposal for any necessary After Sales Support.
Would you like to start an electrification project for your vehicles?
Request a free preliminary assessment and learn how Flash Battery’s lithium batteries can improve your industrial machinery’s performance.
Our Blog
Would you like to talk to us about your electrification project?