Flash Battery commences mass production of lithium modules on its automated line with laser welding technology
16 April 2025
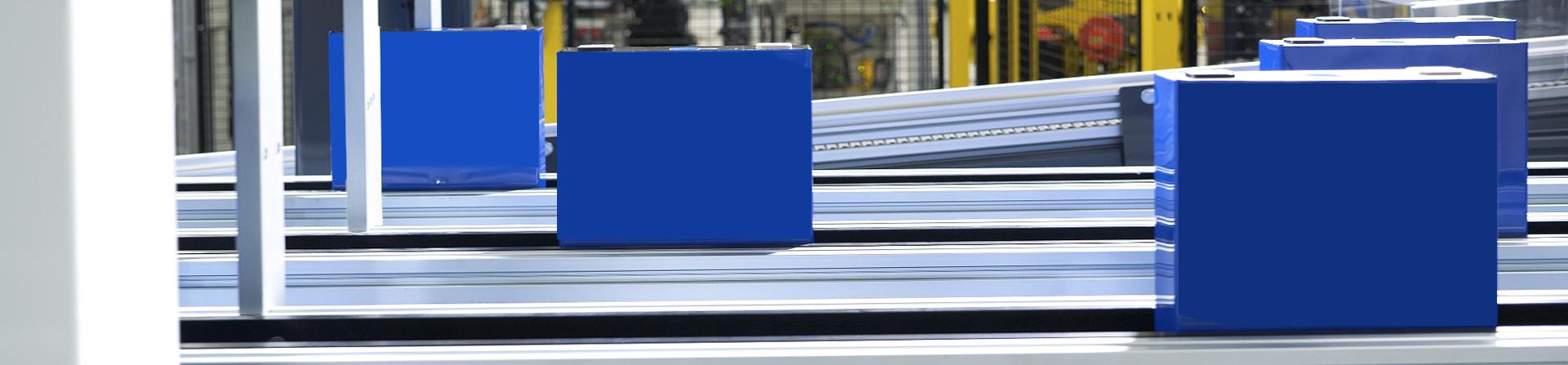
Certain strategic decisions transcend mere investment; they signal a clear commitment to a direction. In 2021, we celebrated the inauguration of our new HQ, a defining milestone marking our transformation from a promising start-up to global industry player. Now, less than four years later, we take another bold step forward with the introduction of our automated lithium module assembly line featuring laser welding technology.
At Flash Battery, growth is driven by foresight—anticipating industry market needs and constantly making investments in innovation. In line with this principle, in 2023, we launched a major expansion initiative, increasing our production area by 2,200 square metres. At its core is an ambitious, future-ready project: a grey room housing an automated module assembly line with laser welding technology—an investment exceeding 6 million euros.
With a production capability of 90,000 modules annually, Flash Battery now operates Italy’s most advanced and highest capacity prismatic cell module assembly line.
This technological leap goes beyond innovation; it represents the organic progression of our working philosophy—internalising key competencies to ensure the highest standards in production.
All industrial expertise centralised in our HQ
Since 2012, we have continuously invested in keeping our expertise within the walls of our headquarters in Reggio Emilia. From our patented BMS to mechanical and electrical design, from prototyping to full-scale production, certifications, process validation, and predictive maintenance—every detail is designed and developed in-house by our team.
The implementation of an automated module assembly line marks a pivotal strategic move for Flash Battery because it allows us to internalise expertise that previously relied on external suppliers, cultivating key skills in-house. Apart from the cells, which we source from the world’s leading manufacturers, this investment completes the puzzle, bringing all production expertise under one roof.
Greater Flexibility
Our line is designed to assemble 13 distinct module configurations. Thanks to meticulous planning and precision in the line’s design, we can transition from producing one module to another within minutes, maximising efficiency.
Reduced Supply Chain Risk
For a cell production gigafactory to remain sustainable and competitive, annual output must reach dozens of gigawatt-hours. As a result, these large-scale facilities primarily cater to the automotive and energy storage industries, where high-volume production is essential.
For a company specialising in producing batteries for industrial manufacturers, internalising module assembly means gaining direct access to the supply chain. Flash Battery sources its cells directly from leading global manufacturers, ensuring multiple suppliers for each type of cell we procure. This approach enhances supply chain reliability and strengthens our purchasing power.
Recent global dynamics have underscored the critical role of direct production control in reducing lead times and overcoming sourcing challenges.
A 100% European Battery
By leveraging our ability to produce modules in-house—and with the anticipated launch of European LFP cell manufacturing gigafactories—we will soon be positioned to offer customers a 100% Made-in-Europe supply, eliminating reliance on non-EU markets.