Lithium batteries for logistics: when sustainable innovation rhymes with efficiency
4 March 2025
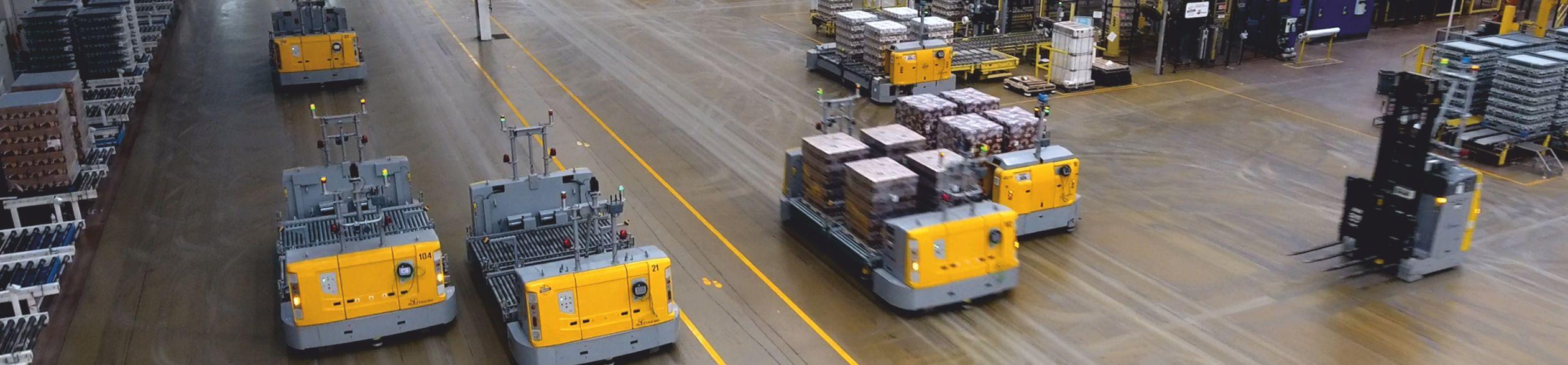
For several years now the logistics industry has been undergoing a profound technological transformation driven by electrification. From forklifts and side loaders to AGVs and LGVs (Automated or Laser Guided Vehicles) used in automated logistics, more and more vehicles in the industry are adopting electrified solutions for greater efficiency, sustainability and reduced operating costs.
This is a change that’s no longer just a trend but an established reality. Indeed, electrification represents the evolution of a sector that sees smart factories as the key to remaining competitive in an increasingly dynamic market.
However, not all electrification technologies are the same. While lead-acid batteries have been the traditional choice for many years, they are now considered obsolete and have largely been replaced by more advanced lithium-ion batteries, which are able to guarantee high performance for a wide variety of industrial vehicles.
But what are the needs pushing the logistics industry to make this change? And what concrete benefits does lithium battery technology offer?
Maintenance time and costs are gone forever!
If there’s one aspect that can have a huge impact on investment choices in logistics, it’s maintenance costs. With the use of conventional lead-acid batteries, time and costs related to routine maintenance are very high: operations such as topping up water and cleaning built-up oxidation and recharging rooms with their air circulation systems increase operating costs and require specially built facilities and dedicated personnel.
Vehicles with lithium batteries, on the other hand, don’t need to stay in dedicated charging rooms and don’t require any routine maintenance. Moreover, when implemented with an intelligent remote monitoring system – as in the case of Flash Battery’s Flash Data Center – they’re subject to predictive, automatic maintenance and constant monitoring of their health status.
Increased energy efficiency
Energy efficiency is a crucial parameter for the operational requirements of vehicles operating in modern automated logistics, demanding increased efficiency with less energy waste. Lithium batteries offer an energy efficiency of more than 96%, compared to 75% for lead-acid batteries.
What does this mean in concrete terms? It means that when you use a lithium battery, almost all the battery’s energy is actually used to power the vehicle. This isn’t the case with lead-acid batteries, where a significant part of the energy is lost as heat, thus generating higher energy costs. Electrification with lithium batteries is thus the ideal choice for those seeking high performance and optimised consumption.
Goodbye battery swap!
Another important benefit of using lithium batteries in automated logistics is the elimination of the need for battery swaps, i.e. the replacement of an empty battery with a charged one.
Due to the long recharging times required by lead-acid batteries, swapping batteries used to be essential to ensure the operational continuity of forklift trucks, AGVs and LGVs operating in logistics facilities. But lithium batteries have revolutionised this limitation thanks to their ability to support rapid charges and opportunity charging during breaks.
This way it’s possible to keep only one battery inside the machine, completely eliminating the space dedicated to recharging rooms and safety risks during battery replacement, with a consequent reduction in structure costs.
Long service life
Last but not least, batteries’ long operational life is a decisive factor in ensuring the efficiency and profitability of logistics operations. Lithium Flash Batteries with LFP chemistry last more than 4,000 recharge cycles, four times more than the 1,000 of lead batteries. Furthermore, lithium batteries with an advanced BMS such as the Flash Balancing System guarantee more stable performance over time.
This means that an AGV, LGV or sideloader equipped with a lithium Flash Battery will be able to operate under intensive conditions for many years without the need to be changed, eliminating replacement and maintenance costs and ensuring greater production continuity, less downtime and a better return on investment. Lead-acid batteries, on the other hand, degrade quickly and lead to loss of range and performance after only a few years of use.
Geographical proximity and a common vision oriented towards innovation have laid the foundation for a solid collaboration that evolved into a true strategic partnership in 2015. This synergy now unites two examples of excellence: the technological know-how of Flash Battery lithium batteries and the sophisticated automation and integration solutions of the E80 Group.
The lithium batteries for AGVs and LGVs developed for the E80 Group have a wide range, from 51.2 V to 102.4 V and from 5.4 kWh to 28.7 kWh of energy, suited for vehicles of all sizes and types. In fact, these vehicles can exceed 1,000 complete cycles of use per year and work non-stop 24/7. Flash Battery technology ensures operational continuity through rapid charging, maximising vehicle uptime without the need for maintenance.
Flash Battery lithium batteries have been installed in more than 5,053 LGVs operating in 326 plants in 42 countries worldwide. Our approach isn’t limited to hardware efficiency. Indeed, we offer an integrated solution through which we can interact directly with LGV/AGVs via remote control and predictive diagnostics, made possible by AI and machine learning algorithms. This solution also includes the possibility of customising the hardware and software to perfectly adapt to the specific needs of industrial facilities.
Our experience in the automated logistics sector thanks to our decades-long partnership with E80 Group has enabled us to fully understand the specific needs of these vehicles and to develop lithium battery solutions over the years that maximise the efficiency of LGVs.
The importance of a tailor-made approach
Customised design allows us to listen to our customers’ needs and build tailor-made batteries respecting the space and dimensions dictated by the vehicle, with voltages, capacities, mechanical and electrical configurations made to measure for the task at hand. But there’s more! We also customise batteries at the software level, including specific features that add value in terms of advanced monitoring, optimisation of charging cycles and predictive diagnostics, thus ensuring maximum operational efficiency and safety.
Safety first
Safety is a key aspect to bear in mind when designing batteries for electric vehicles to be used in logistics facilities.
To ensure maximum safety in every situation, Flash Battery has chosen to use LiFeP04 (LFP) chemistry in all lithium batteries manufactured for AGVs, LGVs and logistics vehicles. In addition to guaranteeing numerous life cycles (>4,000), it is in fact the safest and most stable chemistry on the market because it has a high decomposition temperature and slow heat release, the perfect mix for a superior level of safety.
Moreover, the BMS Flash Balancing system is able to comprehensively monitor the temperature, voltage and internal resistance of each cell, intervening promptly to avoid critical issues. In addition, to further boost safety, the BMS can be integrated with various optional devices: from early gas detection sensors that can anticipate thermal runaways to fire suppression systems.
Your battery, at its best in any weather!
AGVs and LGVs often operate non-stop in logistics facilities with extreme climatic conditions, such as refrigerated warehouses or environments and regions with hot local temperatures. It goes without saying that the inclusion of a thermal management system inside a lithium battery makes it possible for the battery to function in any condition of use.
Flash Battery lithium batteries have an internal intelligence that can control the heating and cooling systems, eliminating all environmental limits and promoting optimal operation at temperatures as low as -30°C or as high as +45°C while maintaining battery efficiency.