Can you trust a high-voltage lithium battery? All the elements that guarantee its safety
12 September 2024
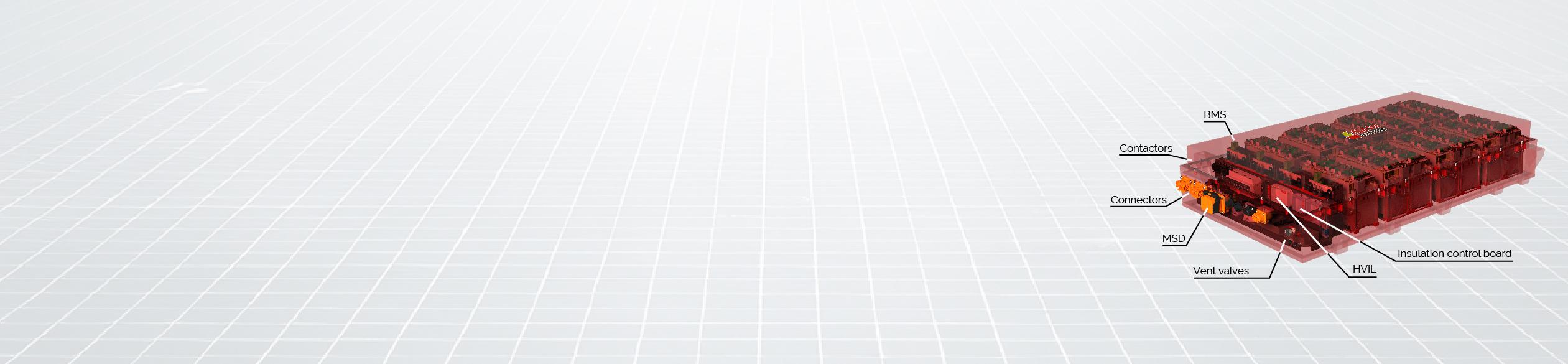
The transition of industrial vehicles to electric power has been under way for some time and is leading to growth not only in the number of electrified applications, but also in their size and power.
Indeed, more and more manufacturers are deciding to support a process of technological conversion, motivated by the many benefits of lithium electrification in terms of Total Cost of Ownership over the long term, sustainability and flexibility of use.
Current technological developments and the great strides made in the sector mean that even those segments with higher power requirements can look to lithium electrification as a viable option for increasing the sustainability and efficiency of their vehicles.
These needs find a concrete answer in high-voltage batteries capable of supporting applications requiring high levels of power and playing a key role in driving the electrical revolution also in these areas of application.
HVIL (High voltage interlock)
The High-Voltage Interlock system (also called HVIL) uses a low-voltage continuous circuit to monitor the proper connection of all high-voltage components within the vehicle.
If the HVIL signal should be interrupted for any reason, the high-voltage supply will be disconnected by cutting off the power in order to safeguard the safety of users.
MSD (Mechanical safety disconnect)
The Mechanical Safety Disconnect (MSD) is a safety device used in high-voltage battery systems to provide a physical method for disconnecting the electrical circuit. The MSD is typically designed to be operated manually to ensure the safety of operators and technicians during maintenance or in emergency situations.
Fuses
Fuses are the simplest and least expensive current-breaking devices, but they can effectively protect the system against overloads caused by short circuits.
The operating principle of a fuse is very simple. It consists of a glass, ceramic or plastic container that contains a conducting element (covered with sand so as to prevent the occurrence of an electric arc) that heats up when current flows through it and that melts due to the Joule effect when it exceeds a certain temperature, interrupting the flow of current.
Insulation control board
The main function of this element is to constantly monitor the insulation resistance between the high-voltage electrical parts of the battery and the vehicle chassis itself. This monitoring helps to ensure operator safety by preventing short circuits and other electrical faults.
Connectors
The connectors in a high-voltage battery differ from the conventional connectors in a low-voltage battery in that they must cover greater insulation distances, prevent direct contact with fingers, and include contacts for the HVIL circuit to pass through to monitor the proper connection.
Contactors
between the battery and the load (as in the case of an electric vehicle’s motor). In emergency situations or in the case of anomalies such as overloads, short circuits, overheating or other, the contactor can open to break the circuit and prevent damage to the battery or system components.
Contactors are essential for opening the circuit even when the vehicle itself is off, thus reducing further risks downstream of the battery. Furthermore, to improve the level of safety more than one contactor is usually used, e.g. one on the positive pole and one on the negative pole, to make sure that at least one is triggered when needed.
“In the beginning we mainly focused on the production of electronics to make our customers’ existing batteries safer and better performing. But we soon realised that the real added value lay in the creation of complete battery packs, which, thanks to the Flash Balancing System, were not only reliable but also intelligent, safe and with a lifetime longer than that of the vehicle they were installed on. The Italian patent for industrial innovation earned by our BMS in 2022 was the culmination of more than 10 years of continuous efforts to make industrial electrification more efficient and safer for an increasing number of applications”.
Predictive maintenance: remote monitoring can anticipate faults
But there’s more! Just imagine the benefits of foreseeing a safety problem even before it occurs. If care is put into its design, a good BMS ensures stable performance over time, prevents faults, and performs self-diagnosis and preventive maintenance, providing a comprehensive check of the battery pack.
Thanks to the Flash Data Center, our remote monitoring cloud system, which uses artificial intelligence and machine learning, you don’t have to wait until it’s too late to notice a problem.
Our AI technology performs real-time collection and analysis of the operating data of all Flash Batteries in the world, and is thus able to proactively recognise potentially abnormal behaviour and communicate it directly to our After-Sales department, which can then take prompt action. This allows the battery’s owner to avoid costly downtimes and much more serious safety problems on vehicles.