Lithium batteries for construction machinery: building sites are choosing the path of electrification
22 October 2024
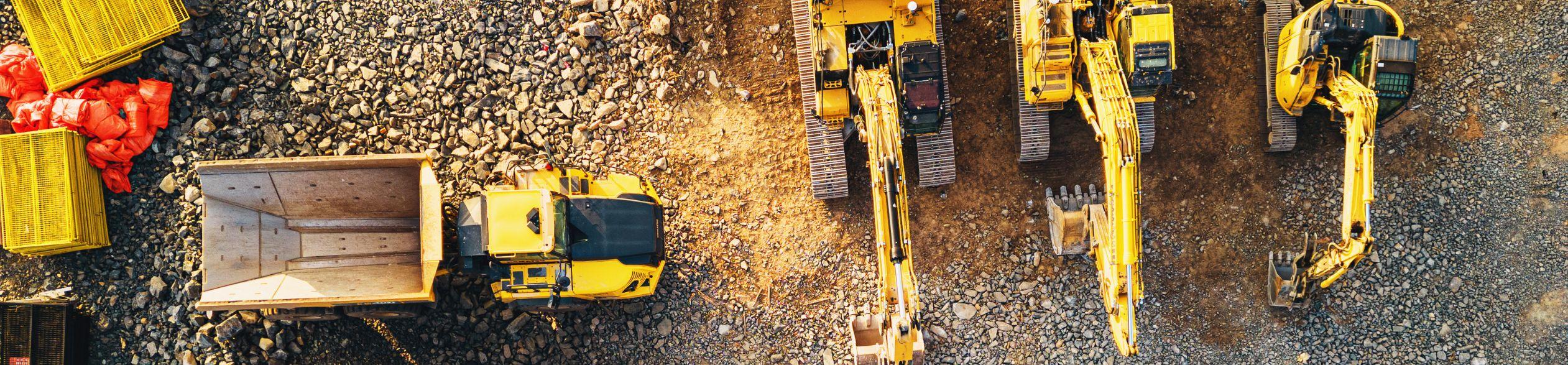
The electric conversion of construction machinery has already been going on for some time now, with the main goal of drastically reducing greenhouse gas emissions and achieving the ambitious goals set by the Paris Agreements. First in line for this process were the more compact machines, but it is also gradually moving into heavier vehicles.
And if building sites, one of the industrial sectors that has always been among the biggest global emissions producers, have chosen the path of electrification, then one question naturally springs to mind: what stage are we at with the technological evolution of lithium batteries and how can they effectively meet the needs of such energy-intensive vehicles?
While up until recently, NMC chemistry was king in the field of construction machinery electrification thanks to its capacity to supply a very large amount of specific energy (220-240Wh/kg), today LFP chemistry is creating an increasingly significant place for itself, focusing on improved energy density up to 190Wh/kg, along with another particularly popular aspect in the sector: safety.
Battery safety: a priority for construction site work
Having access to technologies that improve safety at construction sites is now a strategic lever for the purchasing decisions of any OEMs and producers that have chosen to invest in the electrification of their fleets.
Thanks to their high decomposition temperature and slow heat release, two aspects that help prevent thermal runaway in critical situations, lithium batteries with LFP chemistry are also a winning choice in the construction sector.
This chemistry, together with correct cell assembly and smart control electronics, just like with Flash Battery’s Flash Balancing System, is the perfect compromise between energy and reliability.
In fact, it is best to opt for a slightly bigger battery but one which guarantees high performance and optimum safety, particularly when it comes to the increasingly in-demand high-voltage systems, which can exceed 800V and, if not carefully designed, can pose a real risk for the operator.
Zero emissions for maximum operating efficiency
The race to lower polluting emissions produced by combustion engine vehicles is not just the consequence of the latest European regulations towards decarbonisation: the use of electric machinery not only drastically reduces (if a hybrid is chosen) or completely eliminates (if a full electric model is chosen) CO2 emissions, but also helps optimise work cycles, allowing construction machinery to operate in confined environments as well, for long periods of time, without having to stop to dispel the toxic gases produced by combustion engines.
Another real benefit of lithium batteries in this sector is noise reduction. By getting rid of noise emissions, it creates more flexibility of use in urban areas, as vehicles can operate undisturbed without time restrictions.
While applications under 50kWh have already led the way in converting from combustion to electric, nowadays electrification is also moving into heavier vehicles, drawn by constantly evolving lithium technology, capable of storing an increasing amount of energy in a small space to meet the typical work cycles of construction machinery.
However, due to the specifications of the current technology in terms of energy, volume and charging infrastructure, the full-electric conversion of heavy vehicles, such as large excavators, poses a series of major challenges and, for now at least, remains in the proof of concept phase.
For these highly energy-intensive vehicles that are subject to gruelling work cycles, it is best to opt for a hybrid system, where the battery is used for a few hours and is supported by a motor generator, in order to continue to guarantee a power supply, considering the operations to be carried out and the working conditions.
While we are currently talking about diesel motor generators, in the near future, they could become hydrogen fuel cells, a technology with huge potential, but still being developed.
The road to decarbonisation has therefore also begun for large machinery, but it still has various challenges to face, starting with the lack of charging infrastructure and the difficulty of supporting the power requirements of the demanding work cycles.
Its main features include:
- High energy density
- Option of on-board slow charging and off-board fast charging
- CAN bus diagnostics with optional remote control
- Structure that can withstand vibrations and mechanical stress
- Customised mechanical and electric design
By installing a tailor-made lithium battery, this mini loader can operate more sustainably and quietly, without making any compromises in terms of efficiency and productivity, while maintaining the same performance as its combustion counterpart.
Designed to offer maximum energy density in a small space, this battery has been developed with an extremely customised mechanical design, created to withstand the typical constant stress of the construction site environment.
The energy pack also guarantees up to 8 hours of battery life in energy-saving mode, therefore ensuring that it can keep going for the whole working day with just one quick charge during the lunch break.
Furthermore, the addition of a heating system ensures that the vehicle can also be used in colder climates, while the inclusion of Flash Battery’s proprietary automatic remote control system, the Flash Data Center means it can carry out self-diagnostics and predictive maintenance.
This specific project, just like every customised lithium battery that we make, is therefore the result of in-depth study and a well-established working methodology, which makes us genuine consultants for developing suitable electrification solutions for a wide range of working needs.
Customised consultancy
Before giving the green light to any construction machinery electrification project, here at Flash Battery we pay close attention to an often underrated factor: discussions with the manufacturer.
To be able to manage the project properly, it is essential to understand right from the outset the real operating environment of the application, studying its features and analysing its actual consumption, work cycles, environmental conditions of use, any potential downtime that could be used for fast charging and, last but not least, the conditions of the electric infrastructure and accessibility to the grid.
Prototype creation and production
Only after carefully listening to people’s needs can we actually scale the size of the battery, establishing its capacity and technical specifications and also producing the project’s technical folder, which includes choosing the right mechanical configuration and electrical components.
Once the specific technical dossier has been received, complete with 2D and 3D drawings as well as circuit diagrams, the manufacturer will then be able to officially approve the project and give the green light to the actual prototype production process, setting the supply chain in motion to procure any customised components.
Testing
In no time at all, the battery pack will be ready for the final test bench, which will simulate how the battery operates to check that all the parameters are met and that the battery communicates correctly with the vehicle and charger.
It is an essential aspect, and even more so when you work with high-voltage battery packs, ranging from 24V to over 800V, for which the test phase is a crucially important step to be done with the greatest care and attention.
Operational field analysis
Having also passed the testing phase, the battery pack is ready to be shipped, but Flash Battery’s work does not end here! A crucial phase starts now after delivery: following the customer as they install the system, monitoring tests and assessing the performance in the field, in order to check together that the battery meets expectations and can seamlessly tackle even the harshest conditions of use.
This is the only way that you can successfully launch serial production: a process that will bring an increasing number of vehicles in the construction sector closer to the transition towards zero emissions.