Lithium batteries for Ground Support Equipment: the green revolution promoting airports’ technological transition
24 July 2024
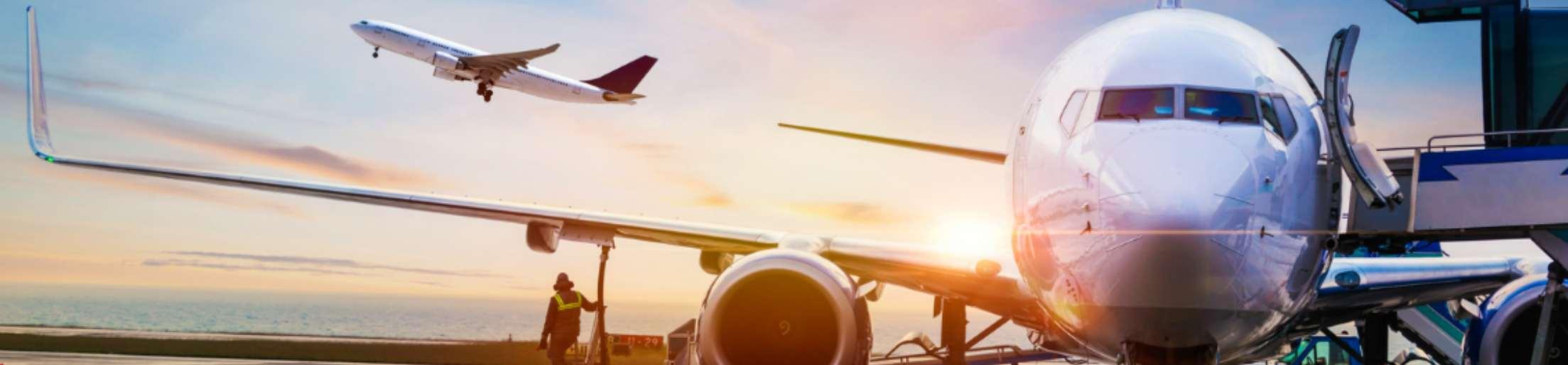
Lowering CO2 emissions and launching a technological transition process at airports has now become a priority for most of the players in this sector, who see the ambitious goals of the European Green Deal not as an obligation, but rather a real lever for increasing the competitiveness of the sector, with the utmost respect for the environment.
Following the setback in 2020 due to the pandemic, the green conversion of airports is now experiencing a major revival: investments are growing and this consequently increases the number of electrified applications. From GPUs up to tow tractors, pushbacks, belt loaders, PRM platforms and boarding stairs, there are many pieces of airport Ground Support Equipment (GSE) that are actively meeting the challenges set by the Green Deal to drastically reduce their emissions by 2030.
Automatic and predictive maintenance side by side in the Flash Data Center’s latest evolution
Breaks are not an option at airports: everything is dynamic, constantly moving, and machines never stop. This pursuit of speed clashes with the limits set by traditional technologies. In fact, lead-acid electrified or internal combustion machines have two major enemies: the need for maintenance and the possibility of encountering long periods of machine downtime in the event of malfunctions.
If implemented with advanced electronics, lithium batteries can overcome this obstacle, thanks to their capacity to perform predictive analysis throughout the life of the application. Flash Battery was one of the pioneers in the field of predictive maintenance, setting up the Flash Data Center in 2013, a proprietary automated remote monitoring cloud system, whose most recent release uses the latest machine learning and artificial intelligence algorithms to learn, analyse and process operating data 24/7 from all the Flash Battery systems active around the world, nipping any potential critical issues in the bud thanks to predictive maintenance and over-the-air updates.
Let’s look at a real-life example: if in Qatar, an operator leaves a tow tractor out in the sun, at an outdoor temperature of 55°C for a long period of time, the system can automatically send a notification to the Flash Battery after-sales department, which will be able to promptly alert the machine manufacturer and resolve this issue remotely before it can actually cause a malfunction in the battery.
Furthermore, OEMs and Ground Handlers can access the portal on their own, at any time, so they can check the state of health of their batteries, analyse big data on all the active systems on their individual machines around the world, but also perform consumption analysis and specific functions for their entire fleet, so they can study the direction of their future investments as best as possible.